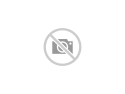
Caterpillar FB85 Feeder Breakers
Ex-showroom Price
Price not available
Variants
Specifications of Caterpillar FB85 Feeder Breakers
Specifications
- Height 0.86 m
- Length 10.36 m
- Width 3.5 m
Dimensions (Approximate)
- Conveyor Width 1422.0 mm
- Discharge Angle: Maximum Dump Position 3.0 Degrees
- Discharge Angle: Minimum Dump Position 1.0 Degrees
- Distance from Discharge to Main Frame 1283.0 mm
- Distance from Head Shaft to Main Frame 1003.0 mm
- Distance Ground to Top of Hopper: Maximum Dump Position 519.0 mm
- Distance Ground to Top of Hopper: Minimum Dump Position 362.0 mm
- Frame Height – Fixed: Maximum Dump Position 1321.0 mm
- Frame Height – Fixed: Maximum Tram Position 1098.0 mm
- Frame Height – Fixed: Minimum Dump Position 864.0 mm
- Frame Height – Fixed: Minimum Tram Position 793.0 mm
- Ground Clearance – Discharge End: Maximum Dump Position 712.0 mm
- Ground Clearance – Discharge End: Minimum Dump Position 304.0 mm
- Ground Clearance – Receiving End: Maximum Tram Position 361.0 mm
- Ground Clearance – Receiving End: Minimum Tram Position 56.0 mm
- Ground Clearance: Maximum Tram Position 361.0 mm
- Ground Clearance: Minimum Tram Position 56.0 mm
- Height of Hopper: Maximum Dump Position 367.0 mm
- Height of Hopper: Minimum Dump Position 337.0 mm
- Height with 152 mm (6 in) Sideboards: Maximum Tram Position 1167.0 mm
- Height with 152 mm (6 in) Sideboards: Minimum Tram Position 863.0 mm
- Length – Front of Hopper to Back Plate 3264.0 mm
- Overall Length 10363.0 mm
- Overall Width 3499.0 mm
- Receiving End Width 3277.0 mm
GENERAL SPECIFICATIONS
- Breaker Diameter 483.0 mm
- Breaker Pick Force (variable) 39916.0 kg
- Gross Vehicle Weight 31750.0 kg
- Intake End Design Ram car, 3 way dump, hopper with sideboards
- Material Compressive Strength (Maximum) 117.0 Mpa
- Material Throughput 860 tonne/hr (950 ton/hr)
- Processed Material Run of mine coal with minimum rock content
- Seam Height 836 mm-1321 mm (34 in-52 in)
- Total Horsepower 150.0 kW
- Tractive Effort 16163.0 kg
- Tram Speed 0-13.7 m/min (0-45 ft / min)
FRAME PLATE SPECIFICATIONS
- Bottom Deck Plate AR steel
- Breakershaft Impact Plate HSLA steel and CCO
- Main Frame Side Plate AR steel
- Top Deck Plate HR steel and CCO
HEADSHAFT SPECIFICATIONS
- Bearing Bore 125.0 mm
- Drive Attachment Method Splined
- Shaft Diameter 127.0 mm
TAILSHAFT SPECIFICATIONS
- Bearing Bore 100.0 mm
- Chain Engagement Roller
- Shaft Diameter 100.0 mm
CRAWLER SPECIFICATIONS
- Drive Method Torque hub, 36:1 planetary reduction
- Freewheel Tow Specification 134 m/min (5 mph) unlimited distance
- Grade (Maximum) 15.0 %
- Ground Pressure 21 445 kg/m2 (30.5 psi)
- Hydraulic Tram Motor Low speed, high torque Geroler 311 cc
- Overload Protection Method – Hydraulic Relief set at 155.0 bar
- Pad Width 381.0 mm
- Parking Brake Yes
- Take Up Method Grease cylinder with steel shims
- Tractive Effort (Maximum) 16163.0 kg
- Tram Speed 0-13.7 m/min (0-45 ft/min )
BREAKERSHAFT SPECIFICATIONS
- Adjustment Method Manually (in increments) 50.0 mm
- Bearing Bore 157.0 mm
- Bit to Flight Clearance 25 mm-127 mm (1 in-5 in)
- Breaker Bit Description Carbide tip hardface protection tapered shank
- Breaker Pick Force (variable) 39916.0 kg
- Breaker Tip to Tip Diameter 483.0 mm
- Breakershaft RPM 61
- Overload Protection Method Underspeed sensor
- Shaft Diameter 203.0 mm
POWER UNIT SPECIFICATIONS
- Drive Chain ASA 180-2 roller chain
- Drive Chain Tensioning Method Grease cylinder with steel shims
- Driven/Drive Sprocket Ratio 27/14
- Electric Motor 200HP/AC/3PH/TEFC/MINE DUTY
- Electric Motor/Pump Coupling Flexible element coupling
- Electric Motor/Reducer Coupling Flexible element coupling
- Gear Reducer 15:1 right angle triple reduction 262 mechanical hp
- Main Hydraulic Pump Axial piston open loop load sense 165 cc
- Overload Protection Method Friction disc clutch and amp overload relay
- Piggyback Hydraulic Pump Priority flow fixed disp. gear 16 cc or 25 cc
CONVEYOR DRIVE SPECIFICATIONS
- Conveyor Chain Speed 0-31 m/min (0-102 ft/min )
- Conveyor Hydraulic Motor Radial piston motor 250 cc
- Gear Reducer 29:1 parallel triple reduction 220 mechanical hp
- Overload Protection Method Hydraulic relief and high pressure switch
HYDRAULIC SPECIFICATIONS
- Control Valve Stack Proportional spool valve load sense 8 section
- Conveyor Circuit Relief Pressure 345.0 bar
- Conveyor Hydraulic Motor Radial piston motor 250 cc
- Heat Exchanger Style Air over oil and/or water over oil
- High Oil Pressure Switch Setting 345.0 bar
- High Oil Temperature Switch Setting 74.0 ° C
- High Pressure Filter 5 micron rating
- Hydraulic Cylinder, Frame Lift and Tilt 305.0 mm
- Hydraulic Fluid Cleanliness Level ISO 4406 16/14/12
- Hydraulic Hose Fitting Type JIC and face seal
- Hydraulic Hose Rating 345.0 bar
- Hydraulic Tram Motor Low speed, high torque Geroler 311 cc
- Main Hydraulic Pump Axial piston open loop load sense 165 cc
- Oil Reservoir 454.0 L
- Oil Reservoir Breather Element 5 micron rating
- Oil Reservoir Power Fill Yes
- Piggyback Hydraulic Pump Priority flow fixed disp. gear 16 cc or 25 cc
- Reservoir Low Oil Level Switch Yes
- Reservoir Oil Thermometer and Sight Glass Yes
- Return Pressure Filter 5 micron rating
- Tram Circuit Relief Pressure 155.0 bar
ELECTRICAL SPECIFICATIONS
- Belt Sequence Sensor 1 Detects operation of the conveyor belt and will stop the conveyor chain when the conveyor belt is not moving.
- Belt Sequence Sensor 2 Restarts the conveyor chain when the conveyor belt restarts.
- Breakershaft Overload Protection Underspeed sensor
- Electric Motor 200HP/AC/3PH/TEFC/MINE DUTY
- Electrical Safety Features – Emergency Stop Button Quantity one, located on main electrical enclosure cover
- Electrical Safety Features – Neutral Start Switch Machine will not start unless tram levers are in neutral
- Electrical Safety Features – Panic Strip, Intrinsically Safe Quantity two, one centrally located on each side of feeder
- Electrical Safety Features – Radio Remote Deadman Switch Remote operation of the machine cannot occur without deadman switch being engaged
- Electrical Safety Features – Siren/Flashing Light 1 The light will flash the entire time there is power on the machine.
- Electrical Safety Features – Siren/Flashing Light 2 Siren will sound upon initial machine start up and prior to each restart of the conveyor chain.
- Electrical Safety Features – Tram/Conveyor Mode Switch Provide lockout of hydraulic: • Tram mode–conveyor function disabled • Convey mode–tram/cylinder function disabled
- High Oil Pressure Switch Yes
- High Oil Temperature Switch Yes
- Main Electrical Enclosure – Circuit Overload Protection Circuit breaker
- Main Electrical Enclosure – Contactor Type Vacuum
- Main Electrical Enclosure – Conveyor Speed Control Potentiometer
- Main Electrical Enclosure – Electric Motor Protection Amp overload relay
- Main Electrical Enclosure – IP 65 rating Dust tight and low pressure wash down
- Programmable Logic Control (PLC) (optional) – Basic Operating Principal of PLC (if equipped) 1 Monitor the operating status of the feeder and warn/shut down when machine damage will occur
- Programmable Logic Control (PLC) (optional) – Basic Operating Principal of PLC (if equipped) 10 Facilitate above ground communication and control through Ethernet connections
- Programmable Logic Control (PLC) (optional) – Basic Operating Principal of PLC (if equipped) 11 Control conveyor speed based on breakershaft electric motor current draw to protect components during high loads & conveyor jams
- Programmable Logic Control (PLC) (optional) – Basic Operating Principal of PLC (if equipped) 12 Conveyor chain speed
- Programmable Logic Control (PLC) (optional) – Basic Operating Principal of PLC (if equipped) 13 Hour meter for preventative maintenance scheduling
- Programmable Logic Control (PLC) (optional) – Basic Operating Principal of PLC (if equipped) 2 Hydraulic oil level
- Programmable Logic Control (PLC) (optional) – Basic Operating Principal of PLC (if equipped) 3 Hydraulic pump suction vacuum
- Programmable Logic Control (PLC) (optional) – Basic Operating Principal of PLC (if equipped) 4 Power consumption
- Programmable Logic Control (PLC) (optional) – Basic Operating Principal of PLC (if equipped) 5 Hydraulic system pressure
- Programmable Logic Control (PLC) (optional) – Basic Operating Principal of PLC (if equipped) 6 Counter for number of times the hauler vehicles dump and time between dumps for statistical data gathering
- Programmable Logic Control (PLC) (optional) – Basic Operating Principal of PLC (if equipped) 7 Hydraulic oil temperature
- Programmable Logic Control (PLC) (optional) – Basic Operating Principal of PLC (if equipped) 8 Component temperatures such as electric motor, gear reducer, bearings
- Programmable Logic Control (PLC) (optional) – Basic Operating Principal of PLC (if equipped) 9 Breakershaft electric motor current draw, 3 phase current and 3 phase voltage
- Radio Remote (Optional) Wireless control of tram, tilt cylinder and lift cylinder sections of the hydraulic valve stack
- Remote Conveyor Start Method Standard – tilt switch; Optional – photo eye, push button station and radio transmitter
- Reservoir Low Oil Level Switch Yes
FIRE SUPPRESSION SPECIFICATIONS
- Activation Points 2
- Chemical Cylinders 2 @ 7.5 kg (20 lb) each
- Discharge Points 8 required
- Manufacturer/Type Approved Ansul dry chemical inspected by certified Ansul technician
- Pressure Cylinders 2 pressure actuators
DUST SUPPRESSION SPECIFICATIONS
- Activation Method Standard – pendulum switch; Optional – electro-hydraulic solenoid activated by forward hydraulic pressure on conveyor motor
- Filtration “Y” strainer at inlet
- Machine Washdown Hose Connected to “Y” strainer clean out connection
- Number of Sprays and Location Six total located at upper hose crossover, three spraying inby and three spraying outby
- Pressure Regulator 0-8.6 bar (0-125 psi)
- Type of Sprays Conical
GREASING SYSTEM SPECIFICATIONS
- Electric Motor and Reducer Manifold Location Near the electric motor and reducer
- Grease Delivery Method Manual
- Main Manifold Location Near the operator’s station
- Main Manifold Serviced Components Tailshaft, breakershaft, and headshaft
- Number of Manifolds Quantity three, main, electric motor and gear reducer
CONVEYOR CHAIN SPECIFICATIONS
- Flight Attachment Method Mounts to extended pins on the chain
- Flight Construction One piece solid barstock
- Flight Dimension 64 mm × 127 mm (2.50 in × 5 in)
- Pin Diameter 24.0 mm
- Pitch 89.0 mm
- Take Up Method Grease cylinder with steel shims
- Ultimate Strength 90720.0 kg
Select Equipment Dealers by Brand and City
Caterpillar FB85 Feeder Breakers Reviews
0.0
Overall
Based on 0 Reviews
Write Review